我国钢铁工业节能减排具有较大的潜力,尤其是烧结、焦化和炼铁这三大工序,其能耗约占全流程钢铁能耗的70%。
近年来,国内外对钢铁工业的节能减排日益重视,节能减排技术取得长足的进步,但由于钢铁生产为长流程工序的特点,生产过程中存在大量的连续、半连续、非连续的物质流和能量流,不同工序衔接、能量的智能调配等方面仍存在很大的能量优化空间。而且,一些余热利用效率更高效的余热利用新工艺技术及装备尚未取得关键性突破,没有得到广泛的推广和应用。因此,国钢铁工业节能减排仍具有较大的潜力,尤其是烧结、焦化和炼铁这三大工序,其能耗约占全流程钢铁能耗的70%本文主要介绍烧结、焦化和炼铁这三大工序的节能减排技术的发展方向及目前存在关键技术问题,希望为钢铁节能减排提供新的解决方案,舞阳钢铁有限责任公司|舞钢钢板|舞阳钢铁|舞阳钢板|舞阳钢铁厂|河钢舞钢|舞钢现货网。
高效炉冷烧结机余热发电技术
技术发展现状
虽然近年来烧结机余热发电技术取得长足的进步,但由于各种原因,烧结机余热发电装置建成后运行效果差,甚至不到设计指标的50%虽经设计及运行单位的不时改进,但始终无法全面快速推广。其主要原因是受烧结机现有环(带)冷方式的限制,烧结机余热发电仍存在很多关键性的难题无法完全解决余热资源是有限的高效利用是关键。改进烧结矿环(带)冷却工艺,采用更为高效的竖炉式冷却,提高烧结矿冷却效率和质量,提高烧结余热回收温度,进而提高余热回收效率,烧结机余热利用技术的发展方向。
工艺系统介绍
高效炉冷烧结机余热发电技术主要分为3个子系统:烧结矿冷却系统、烟风系统和发电系统,工艺流程见图1
图1高效炉冷烧结机余热发电工艺流程图
高效炉冷烧结机余热发电技术具有如下优势:一是提高烧结矿冷却质量。冷却炉设计有预存室,有利于烧结矿温度均化和剩余挥发分析出,可提高烧结矿强度;冷却炉内冷却为等温差冷却过程,可防止热烧结矿因急冷而易裂,提高烧结矿成品率。二是提高烧结矿余热发电能力。烧结矿温度由700℃冷却至150℃,约有80%烧结矿显热被冷却空气吸收,烧结矿余热利用率提高60%获取的余热烟气温度可达600℃左右,烟气品质明显提高;余热发电采用中温中压双压发电系统,朗肯循环效率可提高25%三是降低烧结矿冷却电耗。其解决了烧结矿冷却过程中的漏风问题,而且提高了冷却空气温升,冷却风量仅为环冷方式的1/3左右,可降低烧结机冷却系统自用电。四是减排效果明显。炉冷技术实现了冷却系统的高效密封,设备均为负压运行,解决了环(带)冷方式存在粉尘无序排放的问题。五是提高烧结机运转率和发电系统的平安性。新建的烧结矿炉冷系统与现有的环冷系统互为备用,防止了因冷却系统故障而造成的烧结机生产线的停机,提高了烧结机的年运转率;冷却炉设计有预存段,能够防止因烧结机短时停机造成余热参数动摇,导致发电系统停机的问题,提高了余热参数的稳定性,从而提高了余热发电系统的运转率和设备平安性。
关键技术问题
高效炉冷烧结机余热发电技术优势明显,未来发展的主要方向,但就目前来说,仍存在关键技术问题亟须突破。
基础理论方面0~150mm宽粒径多孔烧结矿在大空腔内的气固逆流移动床流动与阻力特性,导热、对流和辐射耦合作用下的气固间换热特性机理仍须完善;烧结矿在自重作用下的料仓流动特性尚未明确。
工艺技术方面不影响烧结机产量和烧结矿质量的切实有效的炉冷工艺技术方案仍须探索,烧结矿冷却质量、余热获取参数、冷却电耗间的匹配优化技术尚须进一步完善,余热参数与发电系统热力参数的匹配优化尚未明确。
关键设备方面高负载、大倾角、高温物料输送装置尚未幼稚;大空腔烧结矿竖式冷却炉仍须开发,特别是0~150mm宽粒径连续高温烧结矿在大空腔内的均匀布料问题、大空腔内均匀布风问题亟须解决。
工程实施方面新建工程装置、运行不影响烧结机正常生产,降低工程实施费用,提高投资回收效益,这些要求都有待满足,舞阳钢铁有限责任公司|舞钢钢板|舞阳钢铁|舞阳钢板|舞阳钢铁厂|河钢舞钢|舞钢现货网。。
预期效果
如果该技术存在关键技术难题取得根本突破,那么不只可以大幅提高烧结余热回收效率,而且能够提高烧结矿冷却质量,降低污染物排放,经济、社会和环境效益明显。以1条360㎡烧结机配套高效炉冷烧结机余热发电工程为例,钢铁企业每年可对外供电量为12600万千瓦时,可基本满足烧结机生产线用电量,按0.6元/千瓦时电计算,年收入约7560万元,扣除自用电及运行利息约15%电站总投资1.8亿元,缺乏3年即可收回本钱,项目建成后可减少燃煤电厂消耗约5万吨标准煤(电折算标煤系数为0.404年可减排CO2约12.6万吨、减排SO2约1600吨。
荒煤气显热高效稳定回收技术
技术发展现状
炼焦过程中所产生的显热资源利用,已成为提高焦炉效率的主要途径之一。前苏联哈尔科夫炼焦厂最早被报道采用水夹套回收热水作为取暖热源;日本新日铁在焦炉上升管中设置夹套管,采用有机工质回收195℃的热能。国先后开发了导热油夹套管、热管、锅炉等余热回收技术。宝钢针对荒煤气显热回收的难题进行了深入研究,研制了新型上升管换热器,已完成了显热回收利用的方案研究和中试试验工程,具备进一步工程示范的条件。
工艺系统介绍
焦炉荒煤气显热回收工艺系统包括除氧器、除氧水箱、给水泵、循环泵、汽包、加药、取样装置等相关设施。其中汽水工艺流程如图2所示,纯水经过管道先进入除氧器进行除氧,然后通入汽包,液体水进入荒煤气显热回收装置进行荒煤气显热的回收,其产生的汽水混合物进入汽包进行汽水分离,发生的蒸汽被送入蒸汽管网。
图2焦炉荒煤气显热回收工艺流程示意图
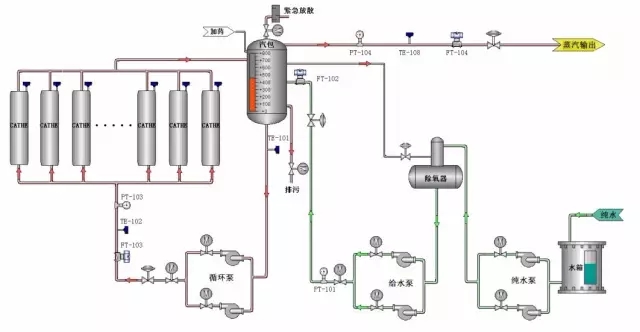
关键技术
焦炉荒煤气显热回收一直是焦化行业节能减排研究热点,其须要解决的主要问题或关键技术包括:复杂工况条件下荒煤气换热计算模型与方法,防腐蚀抗结焦耐高温复合资料技术,狭小空间内上升管换热器强化换热与整体式多重防泄漏结构设计技术,组合式焦炉荒煤气余热回收蒸汽的系统及方法,焦炉上升管换热器在线快速更换技术,下降管换热器显热回收利用关键技术的研究,焦化区域红焦显热、荒煤气显热、烟气余热等能量系统耦合优化节能。
预期效果
宝钢焦炉荒煤气显热回收中试试验研究标明,吨焦回收余热6.8千克规范煤以上,示范工程预计年可回收约8万吨蒸汽,年经济效益为1100万元;扣除自用能耗,年可节约能源约7000吨标准煤。按2013年我国焦炭产量4.76亿吨计算,全部采用上升管高效换热器技术,国年可节约能源320万吨规范煤左右,年节能效益约48亿元,具有良好的经济效益和社会效益。
高炉熔渣余热回收和资源化利用技术
技术发展现状
国内外对高炉熔渣余热回收和资源化利用技术开展了大量研究,高炉渣水淬—冲渣水余热利用,高炉渣干式粒化—余热发电,高炉渣制备水泥填料、矿渣棉及微晶玻璃工艺等成为高炉渣综合利用的主流技术路线。但迄今为止,高炉熔渣热量回收和气淬成珠技术尚未实现产业化应用。
工艺系统介绍
熔渣余热高效回收与生产玻璃微珠工艺流程图如图3所示。
图3高炉熔渣余热高效回收与生产玻璃微珠工艺流程图
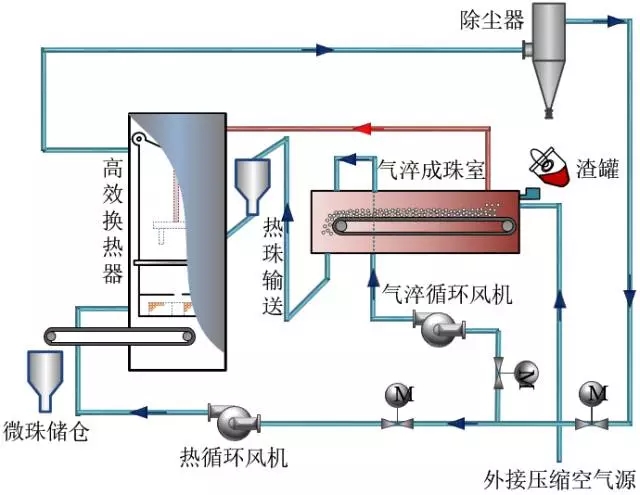
具体流程如下:高炉熔渣经渣罐倒入中间渣槽,通过特制气淬喷嘴粒化成珠,高温渣珠在气淬成珠室与空气完成初步换热后进入高效换热器。换热后的高温气体经管道进入高效换热器,同时渣珠在高效换热器中进行二次换热后进入微珠储仓,热气体和渣珠与锅炉管中的换热工质换热后进入管道再次循环。上述工艺针对高炉炼铁流程特点,实现高炉熔渣余热的梯级利用,同时生产高附加值的玻璃微珠产品。
高炉熔渣余热高效回收与生产玻璃微珠技术具有如下优势:
一是提高余热回收能力。基于熔渣微珠温度分布特点,换热设备设计为无转动部件,并采用辐射段与对流段相结合的换热形式,同时换热工质参数与微珠参数相匹配,保证低成本、低动力消耗、高换热效率和可靠性的同时可实现余热梯级高效回收。
二是提高玻璃微珠成珠率。该技术基于高炉熔渣成分特点,针对高炉熔渣成分调整对气淬成珠过程的影响规律,形成高炉熔渣成分调整与高效生产高质量微珠关键技术,实时保证玻璃微珠高成珠率。
三是气淬过程与余热提取过程良好协同。基于炉熔渣温度、喷嘴结构型式、气淬工艺参数、环境温度条件等多因素耦合作用下传热及成珠规律,该技术解决了当前高炉熔渣余热回收难和熔渣冷却产物附加值低的行业难题。
关键技术问题
高炉熔渣余热高效回收与生产玻璃微珠技术实现了高炉熔渣的能源化与资源化深度利用,具有良好的发展前景,但就目前来说,仍存在3个关键技术问题亟须突破。
一是对高炉熔渣气淬成珠过程换热机制与关键技术进行研究,探索高炉熔渣气淬成珠过程的传热规律,基于气淬过程与余热提取过程,科学协同建立高炉熔渣气淬工艺参数优化模型,形成气淬过程高温余热提取关键技术。
二是研发高炉熔渣余热高效回收工艺,开发出高效颗粒换热设备,对高炉熔渣余热高效回收工艺参数进行优化,形成高余热回收率,同时生产玻璃微珠等建材的新工艺设计方法。
三是建设高炉熔渣余热高效回收关键设备研发与中试生产线,完成气淬系统、余热回收系统、气体循环系统及除尘系统的制造、装置,进行中试实验。
预期效果
如果上述关键技术难题得到解决,就能够形成高炉熔渣气淬成珠与余热回收关键技术和装备,为高炉渣热量回收与高附加值利用提供技术支撑。按2015年全国年产高炉渣约2.4亿吨计算,若20%高炉渣利用该课题研究效果,高炉渣热能回收效率按50%计,则每年回收高炉渣余热折合规范煤约120万吨,预期效益折合人民币约9亿元。同时,制备的玻璃微珠产量约0.28亿吨(成珠率按60%高炉渣高值资源化利用净增利润按100元/吨渣计,预计每年可为国家多创造利润28亿元人民币。项目实施后,每年可节约冲渣新水耗量0.28亿吨左右。
综上所述,钢铁工业作为我国能源消耗大户,节能减排取得了长足的进步,但仍有较大的节能潜力,特别是烧结、焦化、炼铁三大工序。通过对流程工业系统的关键工艺重构、流程再造、系统耦合及参数优化、关键设备研发,突破存在关键技术和设备问题,形成流程工业节能减排整体解决方案,从而可进一步提高钢铁工业的能源利用效率,降低污染物排放,为钢铁流程工业的可继续发展提供科学保证,舞阳钢铁有限责任公司|舞钢钢板|舞阳钢铁|舞阳钢板|舞阳钢铁厂|河钢舞钢|舞钢现货网。。